Understanding Liquid Silicone Rubber (LSR): Applications and Regulations
Silicone rubber, often referred to as medical-grade silicone, is a popular material for various consumer, healthcare, and industrial products. It is favored for its skin-contact safety, durability, flexibility, and softness. However, not all materials labeled “medical-grade” meet the highest standards. To ensure the best quality and safety for our customers, Casco Bay Molding exclusively utilizes full-traceability platinum-cured medical-grade silicone. All our products are manufactured in compliance with ISO:13485 standards, and several of our parts are FDA-registered. Quality is paramount in product development, which is why we exclusively use medical-grade silicone, known as Liquid Silicone Rubber (LSR).
If you’re curious about what Liquid Silicone Rubber (LSR) is and how to determine its medical quality, keep reading to learn how to manufacture top-quality products while adhering to health regulations. If you’re interested in developing a product using medical-grade Liquid Silicone Rubber, Casco Bay Molding is a global leader in silicone injection molding.
Whether you’re a seasoned silicone enthusiast or a newcomer, here’s what you need to know about regulations, distinguishing between different materials, and more.
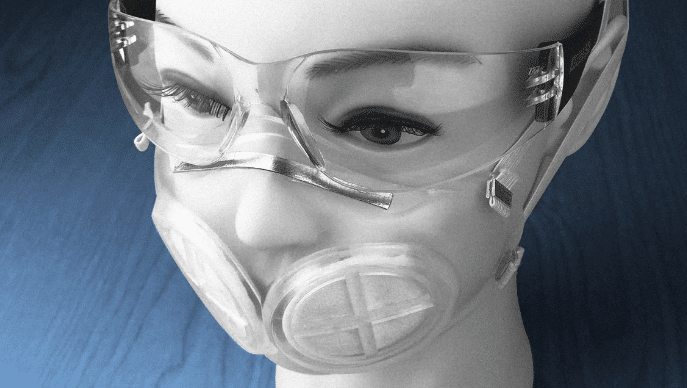
What is Silicone?
Silicone is an elastomer, a rubber-like material that can stretch and then return to its original shape. Technically, it’s a polymer and is renowned for its:
- Non-reactivity
- Flexibility
- Temperature resistance
- Water resistance
- Biocompatibility
The durability, heat tolerance, malleability, and biocompatibility of silicone make it highly desirable for various applications. Medical-grade silicone, in particular, is a favorite in the medical device manufacturing sector and is commonly used in consumer products like cooking utensils, face shields, and scuba gear.
Experts in Medical & Food Grade Silicone
At Casco Bay Molding, we have extensive experience in designing, tooling, and high-volume manufacturing of a wide range of medical, industrial, and consumer LSR parts. Our engineering team boasts decades of product development and injection molding experience with this unique material, and we’re eager to help you bring your medical-grade silicone application to life.
What is Medical-Grade Silicone?
Many companies use the term “medical-grade silicone,” which typically falls into one of two categories:
- Medical-Long Term Implantable Material: This refers to a material that can remain inside the body as part of an implantable device. Due to its high purity, it is generally too expensive for food-grade applications.
- Medical Grade (Medical-Healthcare Grade): Technically known as medical-healthcare grade, Class VI silicone is tested for biocompatibility, making it suitable for a wide range of products, including menstrual cups, baby bottle nipples, scuba mouthpieces, water pipes, and various food and skin contact items. Both Class VI and medical-long term implantable materials are considered safe for food contact and are typically defined as Liquid Silicone Rubber (LSR), which is used for injection molding to create clean, consistent parts.
What is Silicone Made Of?
Silicone is derived from silica, the primary component of sand. Silica, also known as silicon dioxide, contains silicon and oxygen elements. It’s important to note that silicone rubber is not “naturally” derived from sand; it is produced through a chemical process, which means silicone products cannot technically be considered “organic.”
Four Types of Silicone Rubber Available
Commercially, there are four main types of silicone rubber available, each with its distinctive features:
- Liquid Silicone Rubber (LSR): LSR is designed for injection molding and is almost always of medical grade. It is delivered in sealed drums or buckets, one containing a catalyst and the other a crosslinker. LSR has the advantage of being pumped directly from the container into the molding machine with little possibility of material modification, except for the addition of colorants. For this reason, most medical parts are made of LSR.
- High Consistency Rubber (HCR): HCR is a premixed material with a playdough-like texture. It starts as a silicone base stock, to which a catalyst and various fillers/additives are added on a two-roll mill. HCR can be molded into parts or extruded into tubes and may use platinum, peroxide, or tin cure systems. The advantage of HCR is its ability to incorporate different additives or fillers to modify its physical properties. However, it can be disadvantageous if manufacturers don’t disclose the amounts and ingredients of additives and fillers to end-users.
- Fluorosilicone Silicone Rubber (FSR): This flame-resistant, brake fluid-resistant material is primarily used in the automotive industry. FSR offers resistance to compression, stability, and solvents, but it is not employed by Casco Bay Molding.
- Room Temperature Vulcanize Silicone (RTV): RTV solidifies or vulcanizes at room temperature and is typically used for prototype parts. Silicone caulks also fall into this category.
High-Temperature Silicone Curing
Silicone rubber is cured, transitioning from a liquid or gel to a solid state through a chemical process. This process is typically initiated by exposing the material to oxygen, although there are ways to accelerate it. Manufacturers use various catalysts to achieve curing. Liquid Silicone Rubber and High Consistency Rubber cure rapidly when exposed to high heat (around 350°F ± 60°F). At room temperature, LSR may take days to cure, while HCR may take weeks.
Three Common Curing Systems Include:
- Platinum Silicone: LSR is almost exclusively platinum-catalyzed. Properly molded platinum LSR products do not require post-curing. Platinum-cured LSR is generally of medical grade, the choice made by Casco Bay Molding.
- Peroxide: A considerable amount of HCR silicone is peroxide-cured, mainly for extrusion, transfer, or compression molding. Peroxide-cured HCR needs post-baking to remove volatiles, which is a time-consuming and expensive step. Cutting corners during post-baking can lead to remaining volatiles in the material. Peroxide cure systems are generally more cost-effective than platinum systems but necessitate additional time for post-baking.
- Tin Condensation Cure Systems: Tin condensation curing is not recommended for healthcare or medical applications because tin (Sn) remains in the compound after curing.
Is Silicone Plastic? How Do They Differ?
While silicone and plastic are sometimes categorized together as rubbers, it’s essential to recognize their distinct characteristics. Here are a few reasons why we prefer working with Liquid Silicone Rubber (LSR) over traditional plastics:
- Durability: LSR lasts much longer than plastic, making it a more sustainable and higher-quality alternative.
- Biocompatibility: Silicone is more biocompatible, making it safe for use in the body or with food, particularly for sensitive applications like baby bottle nipples and spatulas.
- Non-Formation of Microplastics: Unlike plastic, food-grade silicone does not produce microplastics, which can contaminate water and harm ecosystems.
- Heat Resistance: Silicone is highly heat-resistant, ensuring that no harmful molecules leach into its contents when exposed to heat.
- Versatility: Similar to plastic, food-grade silicone is incredibly versatile and can be molded into various products of all sizes using our expertise in injection molding.
For these reasons, we believe that silicone is a safer choice for numerous sensitive applications compared to other plastic alternatives, such as TPE or latex.